Summing up Taping
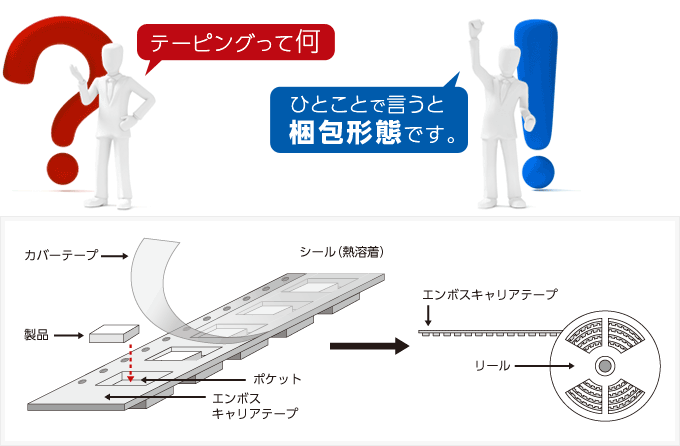
Embossed carrier tape is a packaging format in which concave pockets are made on a chemical product (e.g., resin material) or on long, thin sheets of paper. A product such as an electronic component is placed in each pocket, which is then sealed with cover tape, and the carrier tape is wound around a reel. Taping service also refers to the service of undertaking this packaging work.
JIS standards define the specifications as “JIS C 0806 Packaging of Components for Automatic Handling.”
JIS C 0806 is composed of Parts 1 through 6.
JIS C 0806-1 (Part 1): Tape packaging of components with axial leads on continuous tapes
JIS C 0806-2 (Part 2): Tape packaging of components with unidirectional leads on continuous tapes
JIS C 0806-3 (Part 3): Packaging of surface mount components on continuous tapes
JIS C 0806-4 (Part 4): Stick magazines for electronic components encapsulated in packages of different forms
JIS C 0806-5 (Part 5): Matrix trays (Tentative)
JIS C 0806-6 (Part 6): Bulk case packaging for surface mounting components
JIS C 0806 is composed of Parts 1 through 6.
JIS C 0806-1 (Part 1): Tape packaging of components with axial leads on continuous tapes
JIS C 0806-2 (Part 2): Tape packaging of components with unidirectional leads on continuous tapes
JIS C 0806-3 (Part 3): Packaging of surface mount components on continuous tapes
JIS C 0806-4 (Part 4): Stick magazines for electronic components encapsulated in packages of different forms
JIS C 0806-5 (Part 5): Matrix trays (Tentative)
JIS C 0806-6 (Part 6): Bulk case packaging for surface mounting components
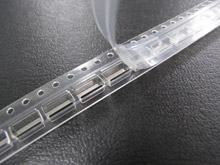
As of April 2013, Parts 4 and 5 have not been established. EPI specializes in providing services for “JIS C 0806-3 (Part 3): Packaging of surface mount components on continuous tapes.”
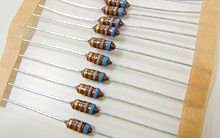
Tape packaging of components with axial leads on continuous tape
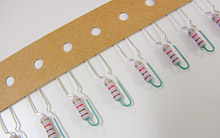
Tape packaging of components with radial leads on continuous tape
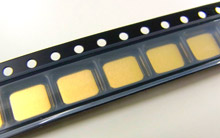
Packaging of surface mount components on continuous tape
EPI has a wealth of human resources, experience, and equipment, with an integrated in-house production system, from equipment to embossed carrier tape production and taping operations.
What is Mounting?
In the electronics field, mounting generally refers to either surface mounting or through-hole mounting.
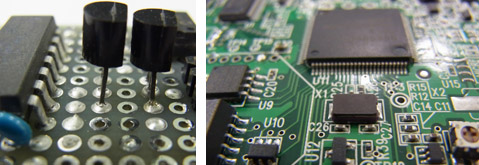
You have probably seen it at least once in an electronic device such as a cell phone or home appliance, or on TV or in a magazine.
Various electronic components are attached to a board called a circuit board or substrate, which is made to perform a desired function. The general term for the process of attaching electronic components to this board and securing them with solder is called mounting.
Through-hole Mounting
The leads (legs) of electronic components are inserted into holes called through-holes and fixed with solder.
This primarily applies to components such as packaged capacitors, which are handled under JIS C 0806-1 (Part 1): Tape packaging of components with axial leads on continuous tapes and JIS C 0806-2 (Part 2): Tape packaging of components with unidirectional leads on continuous tapes.
This primarily applies to components such as packaged capacitors, which are handled under JIS C 0806-1 (Part 1): Tape packaging of components with axial leads on continuous tapes and JIS C 0806-2 (Part 2): Tape packaging of components with unidirectional leads on continuous tapes.
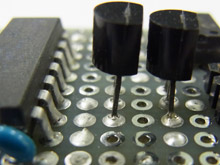
Surface Mounting
Instead of through-holes, electronic components are placed on a printed pattern (a path for electricity to pass through) on the board and secured with solder.
This applies to various electronic components such as packaged ICs, which are handled under JIS C 0806-3 (Part 3): Packaging of surface mount components on continuous tapes.
Most of the small electronic devices that continue to grow in popularity today, such as cell phones, use these surface-mount substrates.
This applies to various electronic components such as packaged ICs, which are handled under JIS C 0806-3 (Part 3): Packaging of surface mount components on continuous tapes.
Most of the small electronic devices that continue to grow in popularity today, such as cell phones, use these surface-mount substrates.
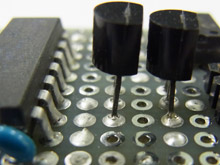
Surface mounting, which involves a large number of components, is performed automatically using a special machine called a mounting machine.
One taped reel is attached to one jig, called a magazine, and the magazine is prepared for the number of parts required.
A few to a few dozen sets of magazines are attached to the mounting machine, which then removes the required electronic components from the embossing and mounts them on the board surface in the required locations and quantities.
In this case, it is important that the embossed electronic components are aligned in a specific direction, including the front and back, top and bottom, and left and right. If there are differences in orientation, the components will be mounted in the wrong direction and won’t be able to fulfill their intended function.
Furthermore, if the cover tape is not attached with a particular level of strength, the mounting machine will not be able to peel off the cover tape properly and will not be able to correctly remove the component from the embossing.
While it may sound simple, if the orientation of each component is not correctly aligned before taping and the characteristics of the embossed carrier tape and cover tape are not accurately captured, it will have a significant impact on the efficiency and cost of mounting.
EPI has a wealth of human resources, experience, and equipment, with an integrated in-house production system, from equipment to embossed carrier tape production and taping operations.
One taped reel is attached to one jig, called a magazine, and the magazine is prepared for the number of parts required.
A few to a few dozen sets of magazines are attached to the mounting machine, which then removes the required electronic components from the embossing and mounts them on the board surface in the required locations and quantities.
In this case, it is important that the embossed electronic components are aligned in a specific direction, including the front and back, top and bottom, and left and right. If there are differences in orientation, the components will be mounted in the wrong direction and won’t be able to fulfill their intended function.
Furthermore, if the cover tape is not attached with a particular level of strength, the mounting machine will not be able to peel off the cover tape properly and will not be able to correctly remove the component from the embossing.
While it may sound simple, if the orientation of each component is not correctly aligned before taping and the characteristics of the embossed carrier tape and cover tape are not accurately captured, it will have a significant impact on the efficiency and cost of mounting.
EPI has a wealth of human resources, experience, and equipment, with an integrated in-house production system, from equipment to embossed carrier tape production and taping operations.
What is Embossed Carrier Tape?
An elongated sheet with concave indentations that are called pockets. The materials used can be broadly classified into paper and chemical products (resin).
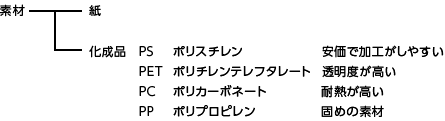
Chemical products also include black sheets with conductive materials mixed into them. Those are used for electronic components that are vulnerable to electrostatic discharge (ESD).
Embossed carrier tape is generally available in widths of 8, 12, 16, 24, 32, 44, 56, and 88 mm.
Width is selected according to the size of the product, but the shape and depth of the pocket is also an important factor in the selection process.
Recently, embossed carrier tape with a width of 4 mm has also been developed to accommodate increasingly smaller electronic components.
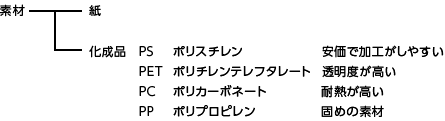
Chemical products also include black sheets with conductive materials mixed into them. Those are used for electronic components that are vulnerable to electrostatic discharge (ESD).
Embossed carrier tape is generally available in widths of 8, 12, 16, 24, 32, 44, 56, and 88 mm.
Width is selected according to the size of the product, but the shape and depth of the pocket is also an important factor in the selection process.
Recently, embossed carrier tape with a width of 4 mm has also been developed to accommodate increasingly smaller electronic components.
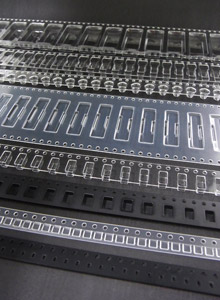
Paper Embossed Carrier Tape
Holes are made in paper that is thicker than the product in order to create the pockets. From there, a paper tape called bottom tape is attached to the back side to complete the process.
It is often used for small electronic components, but it produces paper dust (paper waste). One of the disadvantages of this format is that there are many steps involved in the process, such as opening up the holes and attaching the bottom tape.
などのデメリットがあります。
It is often used for small electronic components, but it produces paper dust (paper waste). One of the disadvantages of this format is that there are many steps involved in the process, such as opening up the holes and attaching the bottom tape.
などのデメリットがあります。
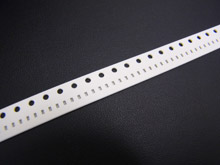
Chemical Product Embossed Carrier Tape
Resin material is softened by heat, and the resin surface is stretched with a mold to shape the pockets.
No paper dust is generated, and a wide variety of materials and widths are available for various applications.
EPI has a wealth of human resources, experience, and equipment, with an integrated in-house production system, from equipment to embossed carrier tape production and taping operations.
No paper dust is generated, and a wide variety of materials and widths are available for various applications.
EPI has a wealth of human resources, experience, and equipment, with an integrated in-house production system, from equipment to embossed carrier tape production and taping operations.
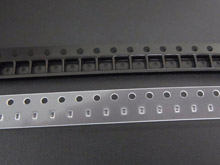
What is Cover Tape?
A sheet of resin used as a lid to prevent products in the pockets of embossed carrier tape from popping out.
The main material used is PET (polyethylene terephthalate). The sheets have a multi-layered structure, with other chemical products applied to the PET.
Typically, during taping the embossed carrier tape and cover tape are heat-welded together by holding them down with a hot iron at a temperature of at least 100°C.
There are also products that stick when a certain amount of pressure is applied at room temperature.
The main material used is PET (polyethylene terephthalate). The sheets have a multi-layered structure, with other chemical products applied to the PET.
Typically, during taping the embossed carrier tape and cover tape are heat-welded together by holding them down with a hot iron at a temperature of at least 100°C.
There are also products that stick when a certain amount of pressure is applied at room temperature.
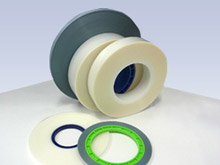
When taping, the cover tape is applied to embossed carrier tape, but various problems can occur if details such as material compatibility, temperature, time, and pressure are not considered.
Peel strength (adhesive strength with the embossed carrier tape) is specified in JIS C 0806-3, and it is important to keep it within that range.
However, even if the tape is kept within that range, if minute problems that cannot be detected by peel strength alone are overlooked, problems may occur during mounting, such as tearing of the cover tape, the cover tape not being able to peel off, or vibration due to uneven adhesion.
This is a process that requires extensive experience and appropriate handling.
EPI has a wealth of human resources, experience, and equipment, with an integrated in-house production system, from equipment to embossed carrier tape production and taping operations.
EPI has a wealth of human resources, experience, and equipment, with an integrated in-house production system, from equipment to embossed carrier tape production and taping operations.
Peel strength (adhesive strength with the embossed carrier tape) is specified in JIS C 0806-3, and it is important to keep it within that range.
However, even if the tape is kept within that range, if minute problems that cannot be detected by peel strength alone are overlooked, problems may occur during mounting, such as tearing of the cover tape, the cover tape not being able to peel off, or vibration due to uneven adhesion.
This is a process that requires extensive experience and appropriate handling.
EPI has a wealth of human resources, experience, and equipment, with an integrated in-house production system, from equipment to embossed carrier tape production and taping operations.
EPI has a wealth of human resources, experience, and equipment, with an integrated in-house production system, from equipment to embossed carrier tape production and taping operations.
What is a Reel?
Reels are used to roll up taped embossed carrier tape.
They are available in external diameters of 180, 254, 330, and 380 mm. The maximum amount that can be rolled up is determined by the size of the product.
Other factors such as production conditions, conditions of use, and handling of the product are also taken into account in the selection process.
Materials used include paper and chemical products, and in some cases they can be reused or otherwise used repeatedly.
They are available in external diameters of 180, 254, 330, and 380 mm. The maximum amount that can be rolled up is determined by the size of the product.
Other factors such as production conditions, conditions of use, and handling of the product are also taken into account in the selection process.
Materials used include paper and chemical products, and in some cases they can be reused or otherwise used repeatedly.
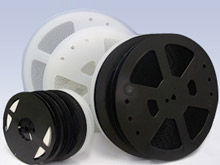
Beyond Electronic Components
Taping was originally created in the electronic components industry as “JIS C 0806 Packaging of Components for Automatic Handling.”
However, we believe there is still a great deal of need in the world for things beyond electronic components, such as “alignment,” “individual packaging,” and “ease of transportation and management.”
For example, in a work process where screws are packed in a box, “If only they were all aligned facing up…”
EPI will address such needs with its integrated system of proposal capabilities and in-house design, development, and production.
If you have any questions or concerns, however large or small, please feel free to contact EPI.
However, we believe there is still a great deal of need in the world for things beyond electronic components, such as “alignment,” “individual packaging,” and “ease of transportation and management.”
For example, in a work process where screws are packed in a box, “If only they were all aligned facing up…”
EPI will address such needs with its integrated system of proposal capabilities and in-house design, development, and production.
If you have any questions or concerns, however large or small, please feel free to contact EPI.